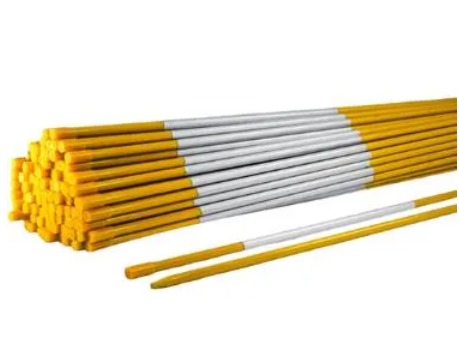
Composite materials have become essential across various industries due to their strength, durability, and lightweight properties. From automotive components to aerospace structures and wind turbine blades, the demand for high-performance composites continues to rise. However, traditional methods of composite production often present limitations in terms of speed, efficiency, and cost. This is where Polyurethane Pultrusion Injection Machine come into play—offering a revolutionary approach to manufacturing composites that dramatically improves performance and productivity.
Understanding Pultrusion and Its Challenges
Pultrusion is a continuous manufacturing process used to produce linear composite profiles with constant cross-sections. Typically, the process involves pulling fibers through a resin bath followed by a heated die where the material cures into its final shape. While effective, traditional pultrusion methods using epoxy or polyester resins often suffer from several limitations such as:
- Slow curing times
- High energy consumption
- Inconsistent material distribution
- Limited mechanical properties
These challenges can affect the quality and scalability of the final composite products. The need for an advanced solution led to the development of Polyurethane Pultrusion Injection Machines, which are rapidly transforming the composite manufacturing landscape.
What is a Polyurethane Pultrusion Injection Machine?
A Polyurethane Pultrusion Injection Machine is a specialized piece of equipment designed to inject polyurethane resin directly into fiber reinforcements before they pass through a heated die. Unlike traditional open bath systems, this closed-injection system ensures precise resin delivery and improved fiber wet-out.
Polyurethane (PU) resin is known for its superior mechanical properties, fast cure time, and exceptional bonding capabilities. By integrating this resin into the pultrusion process through injection technology, manufacturers can produce higher-quality composites with greater speed and efficiency.
Key Advantages of Polyurethane Pultrusion Injection Machines
1. Enhanced Mechanical Properties
Polyurethane resins are known for their excellent tensile strength, flexibility, and impact resistance. When used in pultrusion, they produce composite profiles with significantly higher mechanical performance compared to those made with traditional resins like polyester or epoxy. This makes them ideal for applications that demand high strength-to-weight ratios.
2. Faster Production Speeds
One of the most significant benefits of Polyurethane Pultrusion Injection Machines is their ability to reduce cycle times. Polyurethane resins cure much faster than traditional alternatives, allowing continuous and rapid production. This increased throughput is a game-changer for manufacturers aiming to scale production while maintaining quality.
3. Better Resin Control and Reduced Waste
Closed injection systems provide better control over resin content and distribution within the fiber matrix. This results in less resin waste, improved product consistency, and reduced defects. Precise injection also ensures that every fiber is uniformly coated, which enhances the overall performance of the composite.
4. Energy Efficiency
Because polyurethane cures more quickly and at lower temperatures compared to other resins, less energy is required for the heating and curing stages. This reduction in energy consumption not only lowers operating costs but also supports sustainable manufacturing initiatives.
5. Improved Workplace Safety
Traditional resin baths often emit volatile organic compounds (VOCs), which can be hazardous to workers. The closed system used in Polyurethane Pultrusion Injection Machines significantly reduces VOC emissions, creating a safer and more environmentally friendly workplace.
Applications Across Industries
Automotive Sector
The automotive industry requires lightweight yet strong materials to improve fuel efficiency and vehicle performance. Polyurethane-based pultruded composites are ideal for structural components such as bumper beams, roof panels, and chassis reinforcements. The rapid production capability of these machines makes them perfect for high-volume automotive manufacturing.
Construction and Infrastructure
Pultruded polyurethane composites are used to create durable construction materials like window profiles, handrails, and bridge components. Their resistance to corrosion, UV radiation, and moisture makes them suitable for outdoor and harsh environment applications. The structural integrity and longevity of these composites help reduce maintenance costs over time.
Renewable Energy
Wind turbine blades and other components in the renewable energy sector benefit greatly from the strength and durability of polyurethane pultruded materials. The lightweight nature of the composite contributes to increased energy efficiency and ease of installation.
Electrical and Telecommunications
Insulating materials and cable trays made using Polyurethane Pultrusion Injection Machines offer excellent electrical insulation and fire resistance. These properties are critical in ensuring the safety and reliability of electrical systems and telecommunications infrastructure.
Key Components of a Polyurethane Pultrusion Injection Machine
Injection Head
The injection head is the heart of the machine, where polyurethane resin is precisely metered and injected into the fiber reinforcements. This component ensures accurate dosing and thorough wet-out of the fibers.
Mixing and Metering Unit
This unit is responsible for mixing polyurethane components in precise ratios and delivering them at the required flow rate. Consistent mixing is essential to ensure uniform curing and optimal mechanical properties in the final product.
Heating Die
After injection, the saturated fibers pass through a heated die where the polyurethane resin cures. The design of the die affects the final shape, finish, and dimensional accuracy of the composite profile.
Pulling Mechanism
The pulling system ensures a continuous feed of fiber materials through the machine. It maintains consistent tension and speed, which is critical for producing uniform composite profiles.
Control System
Advanced machines are equipped with programmable logic controllers (PLC) and touchscreen interfaces that allow operators to monitor and adjust process parameters in real time. Automation enhances precision, repeatability, and process stability.
Environmental and Economic Impact
The integration of Polyurethane Pultrusion Injection Machines not only brings technological improvements but also contributes to a more sustainable manufacturing ecosystem. Reduced resin waste, lower energy consumption, and minimized emissions align with global goals for greener production processes.
Economically, these machines offer long-term benefits through lower operational costs, fewer defects, and increased production capacity. Businesses can achieve a faster return on investment while gaining a competitive edge in the composites market.
Future of Composite Manufacturing
As industries continue to demand stronger, lighter, and more durable materials, the role of Polyurethane Pultrusion Injection Machines will only grow. Innovations in machine design, real-time quality control, and digital integration (such as Industry 4.0 compatibility) are expected to further enhance their performance.